Vessels
This research project explores the intersection of slipcasting, mold making, and digital fabrication to develop a series of ceramic vessels. The forms are generated with precise control of the top and bottom profiles of each vessel. Scale, shape and location are modulated to develop a series of sets that uncover subtle shifts in these geometric parameters. The resulting sets are sometimes displayed adjacently and sometimes stacked distributing their profiles vertically as a tall and slender totem.
With the widespread availability of numerically controlled manufacture, design at all scales increasingly relies on countless, mass customized parts. These parts often respond to digital parameters more readily than to material parameters. Design is therefore increasingly responsive to technology rather than tradition. The following design research project attempts to combine tradition and technology in order to study the problem of seriality. The project combines craft traditions with digital techniques to explore a plasticity of parts and their impact on the conventions of material assembly or the making of larger wholes.
Despite the promise of rapid prototyping technologies, casting continues to produce three-dimensional copies (or seriality) more quickly, economically, and durably than rapid prototyping. Mold making and casting play a key role in the production of repeated objects. Beyond the known advantages of serial production such as the interchangeability of standardized parts and the durability of continuous surfaces, the design problem of tooling has received little academic attention. Tooling refers to the molds used to produce copies of components or objects. When reconsidered in light of computation, the mold offers opportunities for design innovation through explorations in plasticity.
murmur: Heather Roberge
In Collaboration with Noa P. Kaplan

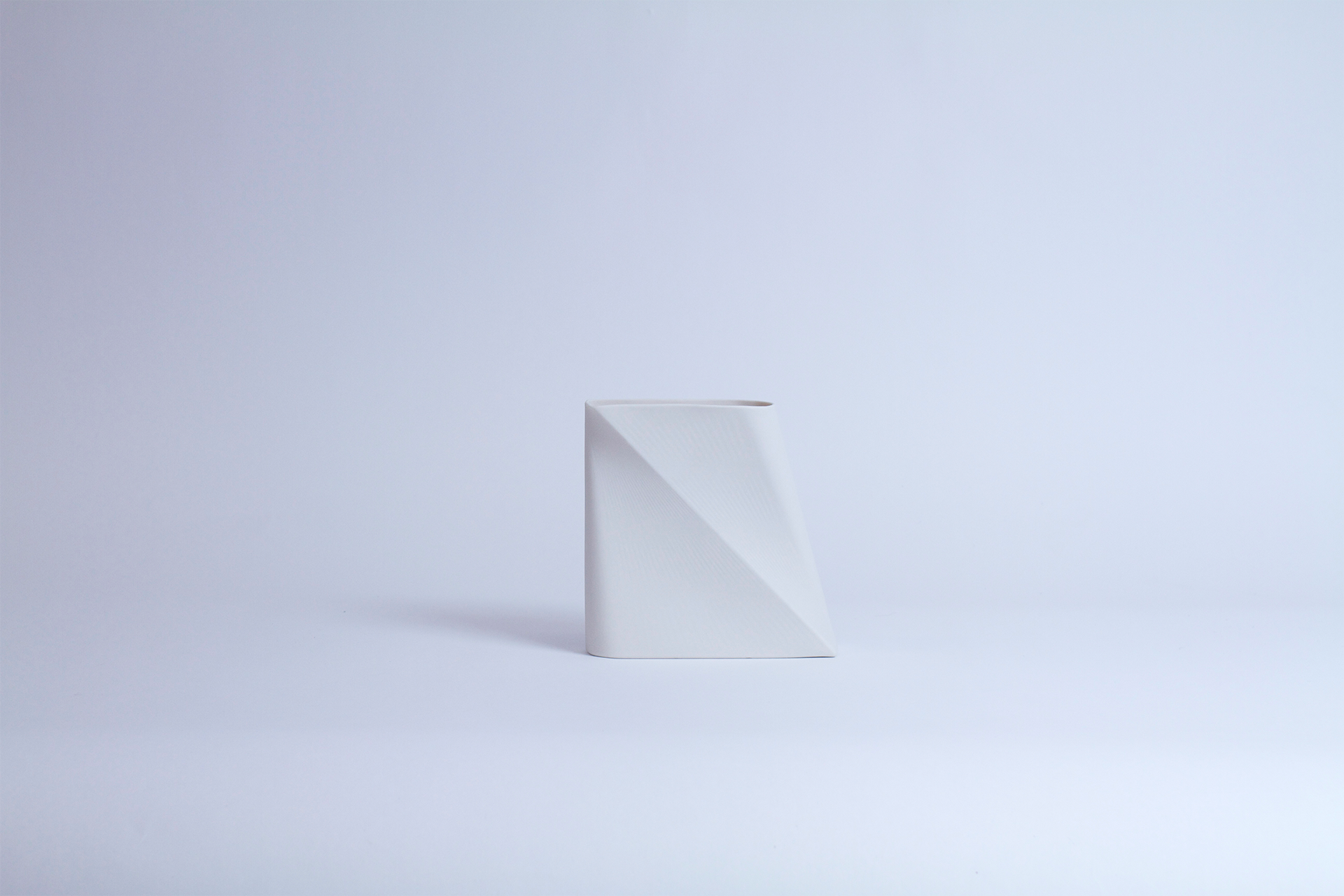




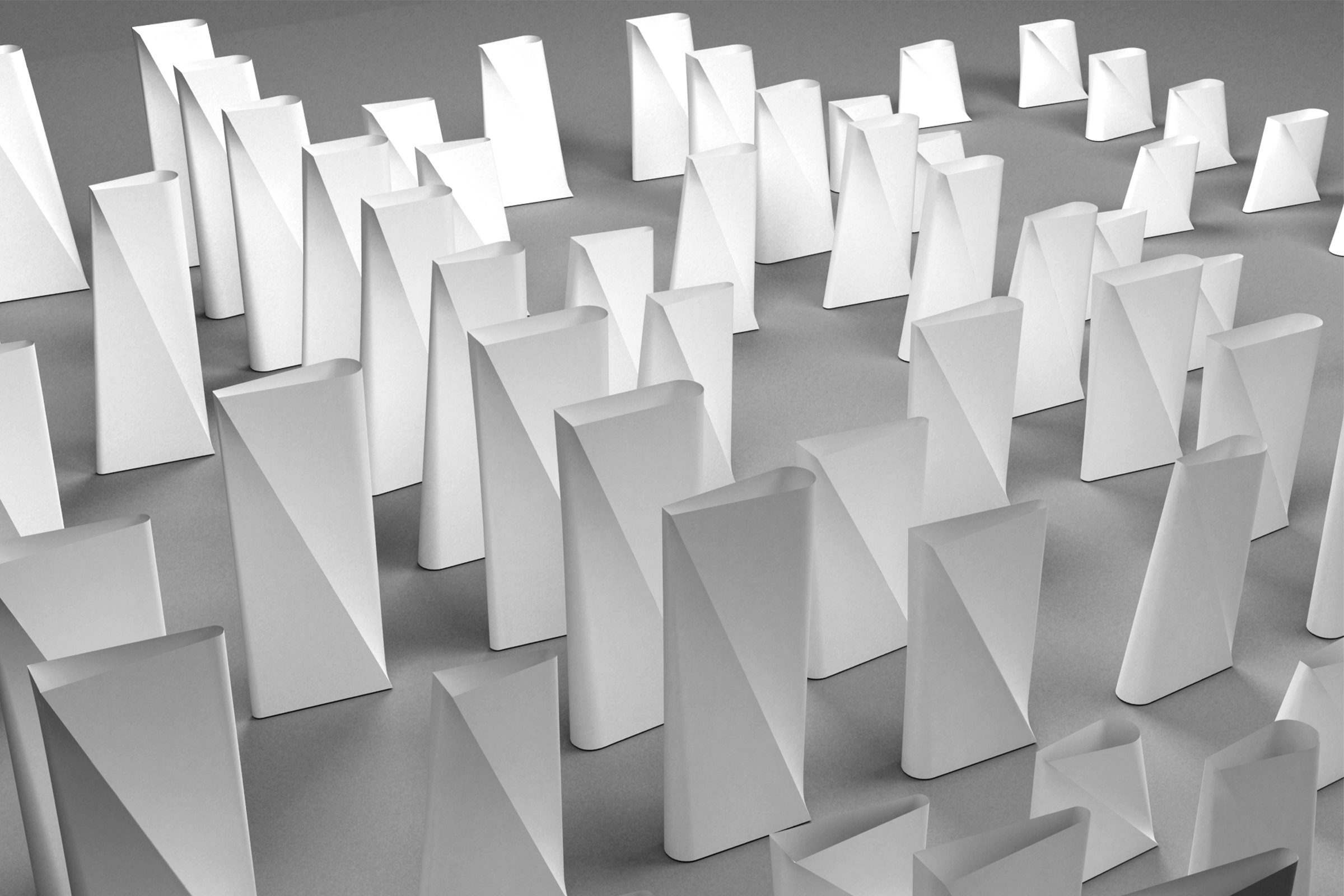
©2025
murmur